Introduction
Exchange
of material between a gas and a liquid plays a very important part in many
chemical processes.
This transfer forms the basis of the unit operations of
distillation, absorption and humidification.
In these cases there is a physical transfer of material across the
phase boundary controlled by the physical properties of the system.
In some instances, physical transfer may he followed by a second
step, chemical reaction, the unit operation then becomes gas-liquid
reaction.
The rate and extent of the reaction and the choice of equipment is
influenced not only by the physical transfer of material but also by the
chemical kinetics.
Garg
produces a range of equipment specially designed for gas-liquid reactions.
The range includes continuous and batch stirred tank reactors,
bubble columns with and without internal fittings, wash, spray and
jet columns.
The Garg units, together with other items such as heat
exchangers, pumps and valves, and our process engineering capability in
the fields of distillation, absorption, extraction, etc. enable us to
design complete systems for laboratory, pilot plant or production use.
Applications
Gas-liquid
reactions may be either spontaneous or initiated thermally,
photochemically or catalytically.
They include processes such as oxidation, halogenation, hydration,
nitration and sulphonation, and are widely used throughout the chemical
industry from petrochemicals to pharmaceuticals. The complexity of the
processes that occur in gas-liquid reactors, involving not only
mass-transfer but also chemical reaction, means that on many occasions
pilot plant studies must be carried out before the production plant design
can be finalised.
The use of glass is an asset at both the pilot plant and production
scale.
- The reacting materials are frequently aggressive.
The wide corrosion resistance of glass makes it an ideal material
of construction. Transparency is a major advantage.
When photochemical reactions are involved, the light source can be
mounted externally and the effect of varying light intensity can be more
readily examined.
In addition to this, the various reaction parameters such as size
of gas bubbles, gas distribution, changes in colour etc. can be easily
observed. Glass is a modular material of construction and the plant can be
easily modified during pilot plant experiments so that an optimal unit
arrangement is achieved.
top
|
|
Selection
of Reactor Type
With
almost all gas-liquid reactions, parallel or series side reactions take
place which lead to unwanted by-products.
This can frequently have a decisive effect on the process
econornies and the correct choice of reactor type and informed process
design is essential.
In
order to achieve the aim of an optimal production unit the process design
engineer needs to know
-
The process chemistry involved including possible side reactions.
- The mechanisms, kinetics and thermodynamics of the reaction occurring.
- The mass-transfer characteristics of the system.
- The characteristics of the reactor and particularly its hydrodynamics in
terms of gas and liquid flows, retention times and distribution.
In
many cases this information is not fully available and laboratory and
pilot plant tests are required using small scale continuous or batch
systems.
These tests can be carried out by our engineers, using customer
materials, in experimental units we have available at our headquarters.
Alternatively units are available to borrow in order for customers
to carry out their own experimental work.
The
following information gives an initial guide to the preferred reactor
type.
-
The stirred tank reactor has a long retention time for the liquid phase.
- The bubble column has a long retention time for the liquid phase.
- The wash and spray columns have short retention times for the liquid
phase.
- The jet column has very short retention times for both the liquid and
gas phases.
In
addition to retention time the initial choice must also be influenced by
the following considerations.
- The gas-liquid exchange surface available which is determined by bubble
size, gas distribution and hold-up.
The
gas-liquid ratio, which can be adjusted to a desired value by recycle if
this does not adversely affect the chemical kinetics.
The
supply or removal of heat, whether an isothermal or adiabatic reaction
cycle is desirable and the influence of the reactor temperature
distribution on the desired product spectrum.
top
|
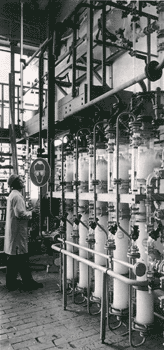
|
Stirred Tank Reactor
The
figure shows a stirred tank reactor which is capable of being operated in
several modes:
-
batch liquid/continuous gas
-
batch liquid/recycle gas
-
recycle liquid/continuous gas
-
recycle liquid/recycle gas
-
continuous liquid/continuous gas
-
continuous liquid/recycle gas.
The
gas may be dispersed in two ways, either using a stirrer or using a Garg gas-mixing valve which is described in detail Heat may be supplied
or removed from the system through the jacket of the reactor or in a heat
exchanger in the recycle line. To enable photochemical reactions to be
carried out submersible lamps may be put into the reactor.
The stirred tank reactor is suitable for
a wide range of applications. It is particularly useful for carrying out
gas-liquid reactions which require a solid catalyst. The laboratory scale
unit
can be used for the determination of kinetic data required for the exact
design of production units.
top
|
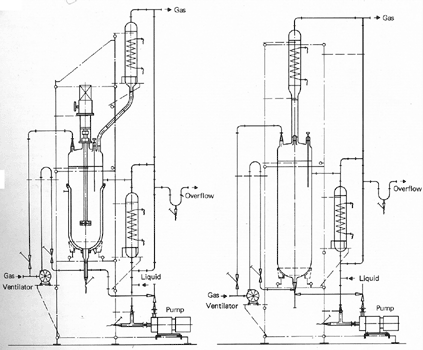
|
Bubble
Column
The
bubble column is predominantly used for continuous operations, in contrast
to the stirred tank reactor it has no moving parts. The unit consists of
an unpacked column section (except that a short packed
section is provided at the top to
remove scum). Gas is
introduced at the base of the column through a gas manifold, or
alternatively using a Garg gas-mixing valve, the gas may be recycled if
required. The liquid can also
be recycled via an external heat exchanger.
Photochemical reactions can be carried out by fitting lights around
the column. Columns of this form have similar retention times to that of a
continuous stirred tank reactor. However,
the continuous stirred tank is a thoroughly mixed system whereas the
column is a dispersed plug flow system.
It is possible to improve the retention time of the liquid phase by
including short packed sections in the column, this however leads to an
increase in back mixing and a reduced gas loading.
top
|
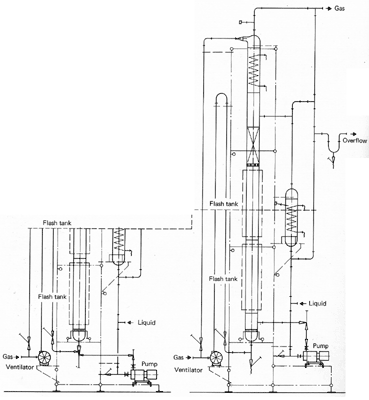
|
Multi - Staged Bubble
Columns
Multi-stage
bubble columns allow greater variation of the retention time of the liquid
phase. The simple construction of
the columns enables a cascade mode of operation to be used, with a well
defined flow path and no remixing between stages. Multi-stage bubble
columns can be supplied with constant or variable bubble formation layer
heights. The column with
constant bubble formation height is based on a filter plate column with
fixed overflow heights and external liquid transfer lines.
In the case of the column with variable bubble layer height, the
liquid outlets are completely flooded and provided with restrictions which
make it possible to adjust the heights of the bubble formation layers
independently of the gas and liquid loadings
. This enables a
mean liquid retention time to be maintained under load changes.
If required heat exchange coils can be fitted in the column and the
temperature profile controlled. Multi-stage bubble columns are an
advantage when an undesirable side reaction must be controlled and they
are particularly suitable
for carrying out physical absorption processes which require stringent
control of the purity of discharge gases.
top
|
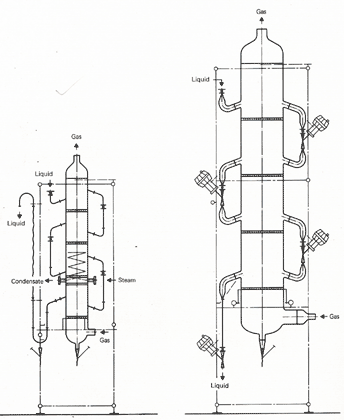
|
Wash and Spray Columns
The
figure shows this very simple unit.
Wash columns are commonly used for purely physical absorption
processes, but they are also suitable for gas-liquid reactions if a short
retention time is required for the liquid phase.
Wash columns are normally operated counter currently.
Co-current operation is possible if the first step in the reaction
is rapid and irreversible.
Co current operation also means that the column can be operated
with higher loadings.
This unit, shown in Figure 1 1 is also used for physical absorption it is
suitable for chemical reactions which require a very short retention time
for the liquid phase.
top
|
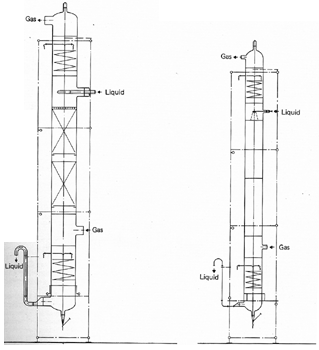
|