Gas absorption
The application of gas absorption techniques in chemical engineering
process operations has expanded rapidly in recent years, particularly in
the fields of exhaust gas scrubbers and the recovery of hydrogen chloride,
hydrogen bromide and oxides of sulphur. In many instances the efficient
recovery of these materials is dictated by economic operating
requirements.
The absorption process relies on the
ability of a liquid to hold within its body relatively large quantities of
a gaseous or vapor component. This ability makes it possible to remove one
or more selected components from a gas stream by contacting with and
absorbing into a suitable liquid.
Whatever type of absorption process is
being considered, in order to achieve efficient gas absorption, the gas
must be brought into intimate contact with the liquid phase. The equipment
must therefore provide a large interfacial area for this contact to occur.
In order to achieve this, several basic designs have evolved.
top
|
Plate Columns
These are very similar in design to
distillation columns and can be fitted with a range of gas liquid
contractors i.e. perforated plates, bubble caps and turbo grids. Columns
efficiencies range from 20-80%. However, plate columns are not
particularly suited for absorption process especially where corrosive
materials are handled.
top
|
Packed Columns
Owing to their design these units are
ideally suited for handling corrosive materials. They have high
efficiencies and are easy to construct and operate.
top
|
Falling Film Absorbers
Falling Film absorption units are very
similar in construction to vertically mounted shell and tube heat
exchangers. The absorbent flows down the walls of the tubes co-currently
with the gas stream. Liquid distribution is provided by a weir arrangement
at the top of the tube bundle. The shell side of the unit contains the
cooling water.
These units are particularly suited for
handling of corrosive materials because of their deign and ease of
operation. They offer the further advantage of being able to handle a wide
range of loadings with a flow rates as low as 24 litres/min/m to maintain
full tube wetting.
All three types of units can be supplied
by us, constructed from Borosilicate Glass.
The main construction material of all
these process plants is borosilicate glass which therefore has the
following particular advantages in the absorption operations.
- It has an exceptional corrosion
resistance to all chemicals, excluding hydrofluoric acid and hot strong
caustic solutions.
- Because of the inertness of the glass, contamination does not occur.
- It is very transparent, therefore any visible malfunctions can be seen
as soon as they occur, Remedial action can be taken without waiting for
spoiled product, or damaged plant to indicate fault.
- Borosilicate glass has very good surface properties, therefore, fouling
within the column on the packing and walls is unlikely.
- All units although designed exactly to customer requirements are of
modular construction. There is therefore minimum outlay in equipment and
plant construction costs.
- Modular construction enables modifications to be carried out easily to
suit changes in operating requirements.
top
|
Exhaust Gas Scrubber
The exhaust gas scrubber represents one
of the simplest forms of the absorption process and is used where
concentrations in the feed gas to the column are low and the component
cannot be economically recovered. As the liquid to gas ratio is normally
high, any heat of solution generated in the process is taken up by the
liquid phase. Heat exchangers to cool the product stream are therefore not
normally required. Absorption is this type of operation can also be
combined with a neutralization process, for example, the use of an
alkaline solution in an acid gas scrubber as shown in the fig.
top
|
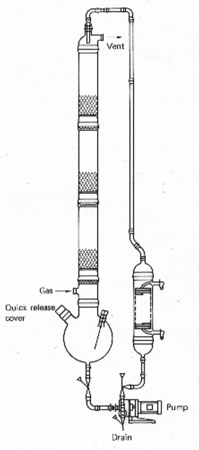
|
Pure Gas Absorber (Constant Feed Rate)
As the feed gas is pure, or contaminated
with air and water vapour only, any vapours generated by the heat of
solution during the absorption process are condensed within the column
itself and are returned with the make up water to the packed section. Any
non-condensibles leave the column by a vent at the top. The product is
cooled by the lower heat exchanger before it leaves the column. Note : -
The acid strength control unit is only applicable in the case of HCl
absorption.
top
|
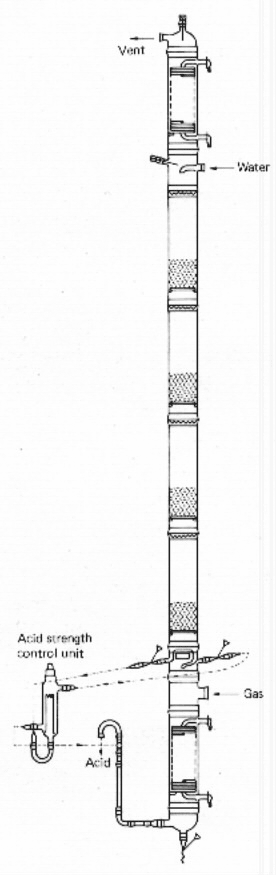
|
Impure Gas Absorber (Constant Feed)
As the feed gas is impure, any vapours
generated by the heat of solution of the absorption process are condensed
externally to the column. The condensate which is usually water and
organic phases are thus removed from the system, ensuring product purity.
The condensate can be treated further to reclaim any valuable material.
The heat exchanger in the base of the column cools the product before it
leaves the unit.
top
|
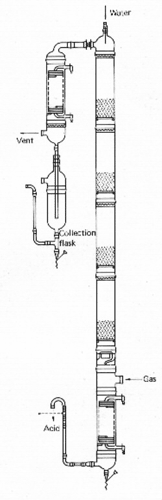
|
Gas Absorber (Varying feed rates)
In certain situations the feed rate of
the gas entering the absorption unit can vary widely, as in a batch
process. For this application a recirculatory system incorporating a
holding vessel is the best solution, where the proportion of feed gas can
be reduced to zero. For this reason the gas loading can be varied between
0-100%, whilst maintaining a fully wetted packing.
The tank is precharged with a calculated
mass of absorbant which is circulated through the column. The gas is
introduced at a point between the two heat exchangers, and rises through
the packing against the falling stream of absorbant. The upper exchanger
removes the heat of solution, the lower one cools the product. An
alternative arrangement, mounting the condenser externally to the column
can be used for contaminated gas feeds.
Once the product in the recirculation
tank has reached the desired concentration it can be discharges and
refilled with absorbant ready for the next operation.
top
|
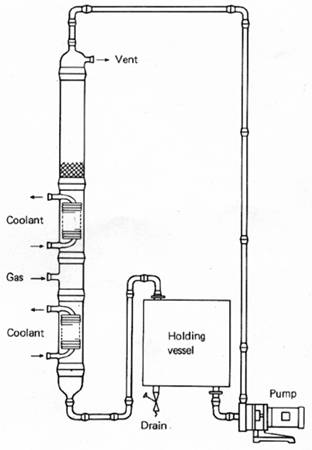
|
Falling Film Absorber
The system consists essentially of a
vertical shell and tube exchanger known as the cooler-absorber, a packed
tail gas scrubber and interconnecting pipe. The gas to be absorbed enters
the system through an inlet at the upper end of the heat exchanger and
flows down inside the parallel tubes with the flow of absorbing liquid.
Unabsorbed gas passes through a riser to the bottom of the tail gas
scrubber. The absorbing liquid is fed through an inlet at the top of the
tail gas scrubber and falls over the packing counter current to the rising
gas. The acid leaving the tower is fed to the top tube sheet of the heat
exchanger. In this way, the heat exchanger works as a number of water
cooled, wet-wall columns in parallel. The falling film absorber is
provided with weirs and an elaborate distribution systems to effect an
equal flow of liquid and gas in each tube. The greatest virtue of the
falling film absorber is its capability to produce strong acid without
detectable vent losses. The Falling Film Absorber can also be used for the
absorption of HCl, HBr, SO2, NH3 etc.
top
|
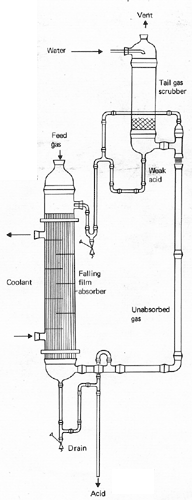
|